Abstract
Cryogenic-assisted machining has already shown its advantages on the process and the machining parameters have been analysed. However, part of the coolant jet characteristics as the pressure and flow rate have not been completely studied and optimized. Hence, the main objective of this study is to investigate the impact of these parameters on tool wear and surface integrity when machining the titanium alloy Ti-6Al-4V. Several nozzle diameters have been therefore employed in order to vary the pressure and the flow rate. A new nozzle holder has been developed to ensure the replacement of these calibrated nozzles of different diameters. The machining tests have allowed to draw attention to the impact of the pressure and the flow rate of the liquid nitrogen jet not only on tool life but also on surface integrity. Indeed, the increase of flow rate and pressure increases tool life. Moreover, surface integrity has been greatly improved notably at the highest pressure and the highest flow rate.
Similar content being viewed by others
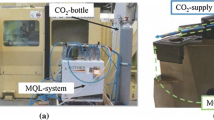
References
Ezugwu E, Wang Z (1997) Titanium alloys and their machinability—a review. J Mater Process Technol 68(3):262–274
Jawaid A, Che-Haron C, Abdullah A (1999) Tool wear characteristics in turning of titanium alloy ti-6246. J Mater Process Technol 92–93:329–334
Rashid RR, Sun S, Wang G, Dargusch M (2012) An investigation of cutting forces and cutting temperatures during laser-assisted machining of the ti-6cr-5mo-5v-4al beta titanium alloy. Int J Mach Tools Manuf 63:58–69
Rashid RR, Bermingham M, Sun S, Wang G, Dargusch M (2013) The response of the high strength ti-10v-2fe-3al beta titanium alloy to laser assisted cutting. Precis Eng 37(2):461– 472
Ayed Y, Germain G, Salem WB, Hamdi H (2014) Experimental and numerical study of laser-assisted machining of ti6al4v titanium alloy. Finite Elem Anal Des 92:72–79
Xi Y, Zhan H, Rashid RR, Wang G, Sun S, Dargusch M (2014) Numerical modeling of laser assisted machining of a beta titanium alloy. Comput Mater Sci 92:149–156
da Silva RB, Machado AR, Ezugwu EO, Bonney J, Sales WF (2013) Tool life and wear mechanisms in high speed machining of ti-6al-4v alloy with pcd tools under various coolant pressures. J Mater Process Technol 213(8):1459– 1464
Ayed Y, Germain G, Ammar A, Furet B (2013) Degradation modes and tool wear mechanisms in finish and rough machining of ti17 titanium alloy under high-pressure water jet assistance. Wear 305(1-2):228–237
Ayed Y, Germain G, Ammar A, Furet B (2015) Tool wear analysis and improvement of cutting conditions using the high-pressure water-jet assistance when machining the ti17 titanium alloy. Precis Eng 42:294–301
Yunlu L, Colak O, Kurbanoglu C (2014) Taguchi doe analysis of surface integrity for high pressure jet assisted machining of inconel 718. In: Procedia CIRP, 2nd CIRP conference on surface integrity (CSI), vol 13, pp 333–338
Braham-Bouchnak T, Germain G, Morel A, Furet B (2015) Influence of high-pressure coolant assistance on the machinability of the titanium alloy ti555-3. Mach Sci Technol 19(1):134–151
Krishnamurthy G, Bhowmick S, Altenhof W, Alpas AT (2017) Increasing efficiency of Ti-alloy machining by cryogenic cooling and using ethanol in MRF. CIRP J Manuf Sci Technol. doi:10.1016/j.cirpj.2017.01.001, http://www.sciencedirect.com/science/article/pii/S1755581717300020
Dhar N, Paul S, Chattopadhyay A (2002) Machining of aisi 4140 steel under cryogenic cooling—tool wear, surface roughness and dimensional deviation. J Mater Process Technol 123(3):483–489
Hong SY, Markus I, cheol Jeong W (2001) New cooling approach and tool life improvement in cryogenic machining of titanium alloy ti-6al-4v. Int J Mach Tools Manuf 41(15):2245–2260
Hong SY, Ding Y, cheol Jeong W (2001) Friction and cutting forces in cryogenic machining of ti-6al-4v. Int J Mach Tools Manuf 41(15):2271–2285
Wang Z, Rajurkar K, Fan J, Petrescu G (2002) Cryogenic machining of tantalum. J Manuf Process 4(2):122–127
Wang Z, Rajurkar K (2000) Cryogenic machining of hard-to-cut materials. Wear 239(2):168–175
Venugopal K, Paul S, Chattopadhyay A (2007) Tool wear in cryogenic turning of ti-6al-4v alloy. Cryogenics 47(1):12–18
Venugopal K, Paul S, Chattopadhyay A (2007) Growth of tool wear in turning of ti-6al-4v alloy under cryogenic cooling. Wear 262(9-10):1071–1078
Dhar N, Kamruzzaman M (2007) Cutting temperature, tool wear, surface roughness and dimensional deviation in turning aisi-4037 steel under cryogenic condition. Int J Mach Tools Manuf 47(5):754–759
Khan AA, Ahmed MI (2008) Improving tool life using cryogenic cooling. J Mater Process Technol 196 (1-3):149–154
Bicek M, Dumont F, Courbon C, Pusavec F, Rech J, Kopac J (2012) Cryogenic machining as an alternative turning process of normalized and hardened aisi 52100 bearing steel. J Mater Process Technol 212 (12):2609–2618
Pereira O, Rodriguez A, Fernandez-Abia A, Barreiro J, de Lacalle LL (2016) Cryogenic and minimum quantity lubrication for an eco-efficiency turning of aisi 304. J Clean Prod 139:440– 449
Dhananchezian M, Kumar MP (2011) Cryogenic turning of the ti-6al-4v alloy with modified cutting tool inserts. Cryogenics 51(1):34–40
Bermingham M, Kirsch J, Sun S, Palanisamy S, Dargusch M (2011) New observations on tool life, cutting forces and chip morphology in cryogenic machining ti-6al-4v. Int J Mach Tools Manuf 51(6):500–511
Shokrani A, Dhokia V, Newman ST (2016) Investigation of the effects of cryogenic machining on surface integrity in end milling of ti-6al-4v titanium alloy. J Manuf Process 21:172–179
Jerold BD, Kumar MP (2011) Experimental investigation of turning aisi 1045 steel using cryogenic carbon dioxide as the cutting fluid. J Manuf Process 13(2):113–119
Machai C, Biermann D (2011) Machining of β-titanium-alloy ti-10v-2fe-3al under cryogenic conditions: Cooling with carbon dioxide snow. J Mater Process Technol 211 (6):1175–1183
Dinesh S, Senthilkumar V, Asokan P, Arulkirubakaran D (2015) Effect of cryogenic cooling on machinability and surface quality of bio-degradable zk60 mg alloy. Mater Des 87:1030–1036
Bordin A, Bruschi S, Ghiotti A, Bariani P (2015) Analysis of tool wear in cryogenic machining of additive manufactured ti6al4v alloy. Wear 328-329:89–99
Bordin A, Sartori S, Bruschi S, Ghiotti A (2017) Experimental investigation on the feasibility of dry and cryogenic machining as sustainable strategies when turning Ti6Al4V produced by additive manufacturing. J Clean Prod 142, Part 4:4142–4151. doi:10.1016/j.jclepro.2016.09.209, http://www.sciencedirect.com/science/article/pii/S095965261631561X
Krolczyk G, Nieslony P, Maruda R, Wojciechowski S (2017) Dry cutting effect in turning of a duplex stainless steel as a key factor in clean production. J Clean Prod 142, Part 4:3343–3354
Maruda RW, Krolczyk GM, Nieslony P, Wojciechowski S, Michalski M, Legutko S (2016) The influence of the cooling conditions on the cutting tool wear and the chip formation mechanism. J Manuf Process 24, Part 1:107–115
Iturbe A, Hormaetxe E, Garay A, Arrazola P (2016) Surface integrity analysis when machining inconel 718 with conventional and cryogenic cooling. Procedia CIRP 45:67–70
Tebaldo V, di Confiengo GG, Faga MG (2017) Sustainability in machining: “eco-friendly” turning of inconel 718. surface characterisation and economic analysis. J Clean Prod 140, Part 3:1567–1577
Pusavec F, Lu T, Courbon C, Rech J, Aljancic U, Kopac J, Jawahir I (2016) Analysis of the influence of nitrogen phase and surface heat transfer coefficient on cryogenic machining performance. J Mater Process Technol 233:19–28
Author information
Authors and Affiliations
Corresponding author
Rights and permissions
About this article
Cite this article
Ayed, Y., Germain, G., Melsio, A.P. et al. Impact of supply conditions of liquid nitrogen on tool wear and surface integrity when machining the Ti-6Al-4V titanium alloy. Int J Adv Manuf Technol 93, 1199–1206 (2017). https://doi.org/10.1007/s00170-017-0604-7
Received:
Accepted:
Published:
Issue Date:
DOI: https://doi.org/10.1007/s00170-017-0604-7