Abstract
Nickel-based superalloy is a typical hard-to-machining material in the aero-engine manufacturing industry. The grindability difference of two kinds of nickel-based superalloys, i.e., equiaxed cast nickel-based superalloy K4125 and wrought nickel-based superalloy Inconel718, are discussed in this article. The influence of grinding parameters (e.g., grinding speed, workpiece speed, and depth of cut) on the grinding force, grinding temperature, and ground surface quality are explored. The results illustrate that under the given grinding conditions, grinding K4125 generates higher forces than Inconel718. The temperature from the K4125 grinding process is beyond 400 °C, while the temperature from grinding on Inconel718 is below 200 °C. Moreover, because of the chip adhesion on the wheel surface when grinding K4125, not only the wheel wear is more severe but also the ground surface of K4125 is worse than that of Inconel718. Accordingly, it could be inferred that the grindability of K4125 is worse than that of Inconel718.
Similar content being viewed by others
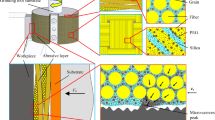
References
Tso PL (1995) Studying on the grinding of Inconel718. J Mater Process Technol 55:421–426
Gift FC, Misiolek WZ, Force E (2004) Fluid performance study for groove grinding a nickel-based superalloy using electroplated cubic boron nitride (CBN) grinding wheels. J Manuf Sci Eng Trans ASME 126(8):451–458
Caruso S, Imbrogno S, Rotella G, Ciaran MI, Arrazola PJ, Filice L, Umbrello D (2015) Numerical simulation of surface modification during machining of nickel-based superalloy. Procedia CIRP 31:130–135
Chen M, Li XT, Sun FH, Xiang Y, Xue B (2001) Studies on the grinding characteristics of dictionally solidified nickel-based superalloy. J Mater Process Technol 116:165–169
Gift FC, Misiolek WZ, Force E (2004) Mechanics of loading for electroplated cubic boron nitride (CBN) wheels during grinding of a nickel based superalloy in water-based lubricating fluids. J Tribol Trans ASME 126(4):795–801
Upadhyaya RP, Malkin S (2004) Thermal aspects of grinding with electroplated CBN wheels. J Manuf Sci Eng Trans ASME 126(2):107–114
Klocke F, Soo SL, Karpuschewski B, Webster JA, Novovic D, Elfizy A, Axinte DA, Tönissen S (2015) Abrasive machining of advanced aerospace alloys and composites. CIRP Ann Manuf Technol 64:581–604
Xi XX, Ding WF, Fu YC, Xu JH (2018) Grindability evaluation and tool wear during grinding of Ti2AlNb intermetallics. Int J Adv Manuf Technol 94:1441–1450
Österle W, Li PX (1997) Mechanical and thermal response of a nickel-base superalloy upon grinding with high removal rates. Mater Sci Eng A 238(2):357–366
Öpöz TT, Chen X (2015) Experimental study on single grit grinding of Inconel 718. Proc Inst Mech Eng B J Eng Manuf 229(5):713–726
Tian L, Fu Y, Xu J, Li HY, Ding WF (2015) The influence of speed on material removal mechanism in high speed grinding with single grit. Int J Mach Tools Manuf 89:192–201
Dai JB, Ding WF, Zhang LC, Xu JH, Su HH (2015) Understanding the effects of grinding speed and undeformed chip thickness on the chip formation in high-speed grinding. Int J Adv Manuf Technol 81(5–8):995–1005
Dai CW, Ding WF, Xu JH, Fu YC, Yu TY (2017) Influence of grain wear on material removal behavior during grinding nickel-based superalloy with a single diamond grain. Int J Mach Tools Manuf 113:49–58
Liu Q, Chen X, Gindy N (2007) Assessment of Al2O3 and superabrasive wheels in nickel-based alloy grinding. Int J Adv Manuf Technol 33:940–951
Chen ZZ, Xu JH, Ding WF, Ma CY, Fu YC (2015) Grinding temperature during high-efficiency grinding Inconel718 using porous CBN wheel with multilayer defined grain distribution. Int J Adv Manuf Technol 77:165–172
Li QL, Xu JH, Su HH, Lei W (2015) Fabrication and performance of monolayer brazed CBN wheel for high-speed grinding of superalloy. Int J Adv Manuf Technol 80:1173–1180
Zhong ZW, Ramesh K, Yeo SH (2001) Grinding of nickel-based super-alloys and advanced ceramics. Mater Manuf Process 16(2):195–207
Xu XP, Yu YQ, Xu HJ (2002) Effect of grinding temperatures on the surface integrity of a nickel-based superalloy. J Mater Process Technol 129:359–363
Ding WF, Xu JH, Chen ZZ, Su HH, Fu YC (2010) Grindability and surface integrity of cast nickel-based superalloy in creep feed grinding with brazed CBN abrasive wheels. Chin J Aeronaut 23(4):501–510
Ding WF, Xu JH, Chen ZZ, Su HH, Fu YC (2010) Wear behavior and mechanism of single-layer brazed CBN abrasive wheels during creep-feed grinding cast nickel-based superalloy. Int J Adv Manuf Technol 51:541–550
Spur G, Niewelt W (1994) Creep feed grinding of Nickel-based alloys with advanced corundum and with CBN-grinding wheels. 7th International Conference on Production/Precision Engineering, Chiba, Japan, 15–17 September 1994
Zhao ZC, Xu JH, Fu YC, Zhang ZW (2013) Creep feed grinding of Ni-based superalloy with micro-crystalline ceramic alumina wheels. Adv Mater Res 797:511–515
Sinha MK, Setti D, Ghosh S, Rao PV (2016) An investigation on surface burn during grinding of Inconel718. J Manuf Process 21:124–133
Yang M, Li CH, Zhang YB, Jia DZ, Hou ZXP, Y L LIRZ, Wang J (2017) Maximum undeformed equivalent chip thickness for ductile-brittle transition of zirconia ceramics under different lubrication conditions. Int J Mach Tools Manuf 122:55–65
Zhang YB, Li CH, Ji HJ, Yang XH, Yang M, Jia DZ, Zhang XP, Li RZ, Wang J (2017) Analysis of grinding mechanics and improved predictive force model based on material-removal and plastic-stacking mechanisms. Int J Mach Tools Manuf 122:81–97
Zhang ZY, Cui JF, Wang B, Wang ZG, Kang RK, Guo DM (2017) A novel approach of mechanical chemical grinding. J Alloys Compd 726:514–524
Heinzel C, Bleil N, Peters J (2007) The use of the size effect in grinding for work-hardening. CIRP Ann Manuf Technol 56(1):327–330
Ghosh S, Chattopadhyay AB, Paul S (2008) Modelling of specific energy requirement during high-efficiency deep grinding. Int J Mach Tools Manuf 48(11):1242–1253
Rowe WB, Chen X (1997) Characterization of the size effect in grinding and the sliced bread analogy. Int J Prod Res 35(3):887–899
Yang SB, Xu J, Fu Y, Wei WH (2012) Finite element modeling of machining of hydrogenated Ti-6Al-4V alloy. Int J Adv Manuf Technol 59:253–261
Chen J, Shi DQ, Miao GL, Yang XG (2017) Effect of maximum temperature on the thermal fatigue behavior of superalloy GH536. Appl Mech Mater 853:28–32
Zhang ZY, Shi ZF, Du YF, Yu ZJ, Guo LC, Guo DM (2018) A novel approach of chemical mechanical polishing for a titanium alloy using an environment-friendly slurry. Appl Surf Sci 427:409–415
Jin T, Cai GQ (2001) Analytical thermal models of oblique moving heat source for deep grinding and cutting. J Manuf Sci Eng Trans ASME 123(2):185–190
Yu TY, Bastawros AF, Chandra A (2017) Experimental and modeling characterization of wear and life expectancy of electroplated CBN grinding wheels. Int J Mach Tool Manu 121:70–80
Zhang ZY, Huang SL, Wang SC, Wang B, Bai Q, Zhang B, Kang RK, Guo DM (2017) A novel approach of high-performance grinding using developed diamond wheels. Int J Adv Manuf Technol 91:3315–3326
Zhou HX, Guo M, Wang XZ (2017) Ultraprecision grinding of silicon wafers using a newly developed diamond wheel. Mater Sci Semicond Process 68:238–244
Mao C, Zhou X, Lin LR, Zhang MJ, Tang K, Zhang J (2016) Investigation of the flow field for a double-outlet nozzle during minimum quantity lubrication grinding. Int J Adv Manuf Technol 85:291–298
Yao CF, Tan L, Yang P, Zhang DH (2018) Effects of tool orientation and surface curvature on surface integrity in ball end milling of TC17. Int J Adv Manuf Technol 94:1699–1710
Butler-Smith P, Axinte D, Daine M, Kong MC (2014) Mechanisms of surface response to overlapped abrasive grits of controlled shapes and positions: an analysis of ductile and brittle materials. CIRP Ann Manuf Technol 63(1):321–324
Chen C, Tang JY, Chen HF, Zhou CC (2017) Research about modeling of grinding workpiece surface topography based on real topography of grinding wheel. Int J Adv Manuf Technol 93:2411–2421
Jia DZ, Li CH, Zhang YB, Yang M, Wang YG, Guo SM, Cao HJ (2017) Specific energy and surface roughness of minimum quantity lubrication grinding Ni-based alloy with mixed vegetable oil-based nanofluids. Precis Eng 50:248–262
Zhang MJ, Tan Y, Zhou FJ, Mao C, Xie ZZ, Li CH (2017) Analysis of flow field in cutting zone for spiral orderly distributed fiber tool. Int J Adv Manuf Technol 92:4345–4354
Acknowledgements
The authors gratefully acknowledge the financial support for this work by the National Natural Science Foundation of China (No. 51775275 and No. 51705463) and the Fundamental Research Funds for the Central Universities (No. NE2014103 and No. NZ2016107).
Author information
Authors and Affiliations
Corresponding author
Rights and permissions
About this article
Cite this article
Qian, N., Ding, W. & Zhu, Y. Comparative investigation on grindability of K4125 and Inconel718 nickel-based superalloys. Int J Adv Manuf Technol 97, 1649–1661 (2018). https://doi.org/10.1007/s00170-018-1993-y
Received:
Accepted:
Published:
Issue Date:
DOI: https://doi.org/10.1007/s00170-018-1993-y