Abstract
Due to low power consumption and fast response, magnetorheological (MR) dampers are widely used in various engineering applications. To enhance the performances, efforts have been made to increase the field dependent force with the same power consumption. However, the fluid viscous force is also increased significantly, which is undesirable in practical use. To tackle this problem, the focus of this paper is to design, simulate, and test an MR damper with multi-grooves (small multiple annular flow gaps) on piston for performance enhancement. First, the detailed design of the proposed MR damper is provided. Then, a coupled field model to describe the characteristics of MR fluid in different regions of MR damper is derived. Based on this model, multiphysics simulations are performed using COMSOL Multiphysics. Parametric analysis of the number and width of multi-grooves is also conducted. Experimental results of the two MR dampers without and with multi-grooves are given and compared with the simulation results. The advantages of MR damper with multi-grooves over the one without multi-grooves and the accuracy of the coupled field model are validated by experiments and simulations. This is the first time that the advantages of MR damper with multi-grooves are validated by experiments. Compared with MR damper without multi-grooves, MR damper with multi-grooves has larger damping force and controllable force range, as well as less increment of fluid viscous force while keeping the same increase of field dependent force. The performance of MR damper with multi-grooves could be further improved by increasing the number and decreasing the width of multi-grooves.
Export citation and abstract BibTeX RIS
1. Introduction
Magnetorheological (MR) fluid, a kind of fluid with ferrous particles immersed in oil medium, has many engineering applications. The magnetic particles dispersed in the MR fluid, form chain-like structures in milliseconds when magnetic field is applied, so as to generate controllable yield stress. Taking the advantages of MR fluid, MR dampers meet the requirements of various application systems or devices with rapid response, controllable damping force or torque, simple structure, and low power consumption [1–5].
The common applications of MR dampers include vibration control, rehabilitation medical devices, energy harvesting, etc. Due to its high damping capacity, low cost and robustness, many control devices using MR dampers were implemented to control undesirable vibrations. Sun et al [6] developed a seat suspension system working with a rotary MR fluid damper for heavy duty vehicles under fuzzy logic control. Christie et al [7] proposed a pendulum tuned mass damper with MR fluid for reducing seismic vibration. In our group, MR dampers were used in train suspension systems in which feasibility, model and control were studied [8], and MR damper was designed and tested [9]. Recently, Jin et al [10] also developed an MR semi-active suspension system with variable stiffness isolators and variable damping dampers to improve ride comfort for high-speed trains. Additionally, MR dampers are also good candidates for vibration control in tunnel boring machine [11], spacecraft [12], aircraft landing gear [13–15] and civil structures [16], etc. As for rehabilitation medical devices, MR dampers can provide controllable force or torque so that the limbs of patients can move in the way similar to healthy people. Park et al [17] developed a prosthesis operated in active (driven by electronically commutated (EC) motor) and semi-active (driven by MR damper) modes. Gao et al [18] proposed a smart prosthetic knee utilizing an MR damper, a direct current (DC) motor, and springs, in which the MR damper was controlled to hold the springs to store and release mechanical energy. Jiang et al [19] and Jing et al [20] designed and tested a robotic leg using MR fluid with tunable stiffness for terrestrial locomotion. Xu et al [21] presented a robotic system equipped with MR actuators, in which the MR actuators transfer the torque to robotic joint in the robot-active mode and provide resistance to help strengthen muscles in human-active mode. Moreover, energy harvesting modules are integrated into MR damper to make it self-powered or self-sensing. Guan et al [22] proposed a compact MR damper with self-powered capability, combining a ball-screw-based regenerative device with a conventional linear double-ended MR damper. Zhu et al [23] designed a long stroke stiffness controllable MR damper with self-powered generation capability. Chen et al [24] proposed and investigated a self-sensing MR damper with power generation, which integrated energy harvesting, dynamic sensing and MR damping technologies into one device.
In order to increase the damping force or torque of MR damper with the same power consumption (improve energy efficiency), some methods were used, such as inner bypass [25–28], annular-radial ducts [1], multi-pole [29, 30], various types of flow channels [31, 32], permanent magnets [33–35], etc. Although the field dependent force increases with these methods, the fluid viscous force also increases significantly, which is one of the major deficiencies of many MR dampers. Bai et al [36] designed an MR damper with inner bypass, in which the field-dependent force could be increased while the viscous damping force was minimized via multiple magnetic circuits. However, the maximum working stroke of the prototype was significantly reduced due to the increment of piston length.
Gavin [37] designed multi-duct electrorheological dampers by a set of concentric metallic tubes. Then, Namuduri et al [38] introduced similar design to MR damper and proposed an MR damper with multiple concentric annular flow gaps. The damping force, turning-up ratio (dynamic range), and linearity of the damping force response were significantly improved. Later, Goldasz [39] built the mathematical model for MR damper incorporating parallel multiple flow paths in the piston and performed relevant simulations. Based on this kind of design, Bai et al [40] proposed an MR energy absorber with dual concentric annular valves. Permanent magnet was utilized between the annular valves for fail-safe, and the damping force could be increased (decreased) by applying positive (negative) currents to the coil. This kind of MR damper is renowned for its low off-state damping force (fluid viscous force) compared with the normal one with single annular flow gap. However, the efforts in MR damper with multiple annular flow gaps were focused on modeling and simulation, and no prototype was fabricated and tested.
Suppose that if the width of the multiple annular flow gap becomes smaller, what will happen? If the gaps are very small, the fluid viscous force may become much smaller than that of gaps in normal sizes. To address this issue, the multiple annular flow gaps are made small, the so-called 'multi-grooves', and a new MR damper with multi-grooves on piston is now proposed. This is the first time that the prototype of MR damper with multi-grooves (small multiple annular flow gaps) is fabricated and tested. With this configuration, larger damping force and controllable force range, as well as less increment of fluid viscous force while keeping the same increase of field dependent force can be obtained compared with MR damper without multi-grooves.
Unlike multi-grooves in the form of small multiple annular flow gaps, utilization of multi-grooves in other forms on MR damper was found in the work of Yoon et al [41] and Strecker et al [42]. Yoon et al [41] machined multi-grooves on the inner surface of the damper housing to reduce eddy current magnitude and thus response time. Strecker et al [42] used selective laser melting technology to print structured magnetic cores (bobbin and outer cylinder) optimized for low weight and homogeneous magnetic flux density in the gap. The fabricated MR damper had low eddy-current losses (fast response time), high magnetic flux (high dynamic force range), low weight and good mechanical properties.
In this paper, an MR damper with multi-grooves on piston is designed, simulated, fabricated, and tested. The major advantages of MR damper with multi-grooves over the one without multi-grooves are: (a) larger damping force and controllable force range; (b) less increment of fluid viscous force while keeping the same increase of field dependent force. The proposed coupled field model accurately characterizes the behavior of MR fluid. Based on this model, the parametric analysis shows that increasing the number and decreasing the width of multi-grooves can further improve the performance of MR damper. The rest of the paper is organized as follows. The design methodologies and details of the proposed MR damper are provided in section 2. Then, in section 3, a coupled field model to describe the behaviors of MR fluid in different regions of MR damper is derived and incorporated into COMSOL Multiphysics for simulations. Parametric analysis of the number and width of multi-grooves is also performed. Furthermore, the testing results of the two MR dampers without and with multi-grooves are given and compared with the simulation results in section 4. Finally, relevant discussions and conclusions are made in sections 5 and 6, respectively.
2. Designs of MR dampers
This work is an extended research of Gao et al [18], and the MR dampers here are designed based on the previous prototype. The previous prototype was a cylindrical and double-ended one without accumulator for prosthetic knee. MR fluid was filled in the cylindrical tube and worked in flow mode. Some key dimensional parameters were optimized using particle swarm optimization (PSO) algorithm. The geometric illustration of the previous prototype is depicted in figure 1, and the optimized dimensional values are listed in table 1. The damper housing and piston were made of silicon steel in view of its large relative magnetic permeability, while the piston rod and damper cover were made of aluminum for magnetic insulation. The magnetic circuit is illustrated in figure 1 as red dashed lines.
Figure 1. Geometric illustration of the previous MR damper prototype.
Download figure:
Standard image High-resolution imageTable 1. Optimized dimensional values of the previous MR damper prototype.
Parameters | Values (mm) |
---|---|
Length of damper housing ![]() | 80 |
Length of piston ![]() | 26.1 |
Length of front/rear piston head ![]() | 9.6 |
Outer radius of damper housing ![]() | 22.2 |
Radius of piston rod end ![]() | 3 |
Radius of piston rod ![]() | 6 |
Radius of front/rear piston head ![]() | 18.6 |
Radius of middle coil ![]() | 16 |
Inner radius of damper housing ![]() | 19.7 |
Radius of middle piston ![]() | 11 |
Housing thickness ![]() | 2.5 |
Annular duct gap ![]() | 1.1 |
Coil radius ![]() | 0.21 |
The focus of the new design is the structural improvement of the piston. In order to ameliorate the MR fluid flow field to obtain larger damping force of the MR damper, a new design of the piston is now proposed. Circular multi-grooves are fabricated on the outer edge of the front and rear piston heads. The multi-grooves function as circular through holes. When the piston moves, the MR fluid flows through the multi-grooves on the front piston head to the middle coil region, and then flows through the multi-grooves on the rear piston head.
Currently, there are two layers of multi-grooves. As for the dimensions of the multi-grooves, the previous annular duct gap is separated as new annular duct gap
, the first layer width
and the second layer
. The following relationship holds:

Figure 2 shows the structural illustration of MR damper piston without multi-grooves (previous design) and with multi-grooves (new design). Figure 3 shows the magnetic circuit of MR damper with multi-grooves. The original annular duct gap is divided as the new annular duct gap, the first- and second-layer multi-grooves, and other geometric dimensions remain the same. Additionally, the thicknesses of the two walls to make the multi-grooves are so small, the decrease of the total length of the magnetic circuit can be neglected. Therefore, the total effective length of the magnetic circuit could be considered the same as the MR damper without multi-grooves. The new annular duct gap and multi-grooves are beneficial for magnetic field passing through the MR fluid.
Figure 2. Structural illustration of MR damper piston without multi-grooves and with multi-grooves. (A) Without multi-grooves; (B) with multi-grooves.
Download figure:
Standard image High-resolution imageFigure 3. Magnetic circuit of MR damper with multi-grooves.
Download figure:
Standard image High-resolution imageAs for the realization of multi-grooves on the piston, four circular rings (two small rings, two large rings) made of silicon steel whose thicknesses are and two cross supporters made of magnetic insulated steel are fabricated. A piston with eight convex supporters and of smaller radius (18.1 mm) is also machined. The four circular rings are installed around the front and rear piston heads and supported by the convex and cross supporters. AB glue is applied at all supporting locations. The detailed structures of multi-grooves on the piston are shown in figure 4.
Figure 4. Detailed structures of multi-grooves on the piston. (A) 3D model; (B) fabricated parts; (C) assembly.
Download figure:
Standard image High-resolution imageFigure 5 describes the structures of the MR damper with multi-grooves. Prototype of MR damper with multi-grooves is fabricated and assembled. Meanwhile, another prototype of MR damper without multi-grooves whose dimensions are the same as the one in Gao et al [18] is also fabricated and assembled, as shown in figure 6. It should be noted that the MR fluid used here is MRF-132DG from LORD Corporation. The turns of the copper coil are 162 as suggested in the previous work. In the two prototypes fabricated, the upper and lower piston rods are aluminum rods covered by polytetrafluoroethylene (PTFE) tubes, and the small seal rings are made of fluoroelastomer (FKM). This combination was aimed to decrease the mechanical friction force due to the low friction characteristics of these two materials [17]. In the following sections, the performances of these two MR dampers will be compared in simulations and experiments.
Figure 5. Structures of the MR damper with multi-grooves.
Download figure:
Standard image High-resolution imageFigure 6. Fabricated parts and assemblies of MR dampers without and with multi-grooves. (A) Fabricated parts; (B) assemblies.
Download figure:
Standard image High-resolution image3. Simulations of MR dampers
Before testing the two MR dampers, simulations are performed to investigate their performances and validate the effectiveness of the proposed design and configurations. In the previous studies on MR dampers, simulations were mainly focused on distributions of magnetic field, in which MR fluid is treated as a normal medium for magnetic conduction. However, MR fluid is intrinsically a kind of viscous fluid whose viscosity changes with the applied magnetic field. The correlation between fluid and magnetic field can be described by the viscosity of MR fluid. When there is no applied magnetic field, the viscosity of MR fluid is constant. When magnetic field is applied, the viscosity of MR fluid increases, which partly contributes to the on-state damping. In addition, when MR fluid flows, the magnetic field distributions will be influenced as well. As a result, simulation of MR fluid should consider the double-sided magnetic fluid interaction.
The core calculation procedures are as follows. When magnetic field is applied, the viscosity of MR fluid is determined by certain relationships. With the calculated viscosity, the fluid motion is then obtained by solving Navier–Stokes equations. With the piston moving and the MR fluid flowing, the magnetic field is calibrated and recalculated simultaneously. Then the viscosity of MR fluid is updated repeatedly using the recalculated magnetic field.
As mentioned above, the relationships between the viscosity of MR fluid and applied magnetic field are quite crucial in simulation. Some researchers have already done some pioneer work regarding the modeling of MR fluid using computational fluid dynamics (CFD). Susan-Resiga [43] proposed a rheological model by combining a quasi-Newtonian behavior at very low shear stress with a Herschel–Bulkley model for large shear stress value, which could be used in regular CFD codes to compute the MR fluid flow. However, no simulation results were provided. Parlak et al [44, 45] built a Bingham CFD model based on the Bingham plastic model in which critical point was defined between Newtonian (no magnetic field) and non-Newtonian (applied magnetic field) regions. Simulations results derived by ANSYS CFX were in good agreement with the experimental data. A modified Bingham model for COMSOL Multiphysics was proposed by Case et al [46] and further extended by Zheng et al [47]. In this model, the transition from Newtonian to non-Newtonian regions were described by continuous function using two parameters (no critical point), which facilitated calculations and showed good robustness. Recently, Elsaady et al [48] proposed a one-way coupled numerical approach (ANSYS Fluent + COMSOL Multiphysics) to model the dynamic hysteretic behavior of a twin-tube MR damper.
In this section, the relationships between the viscosity of MR fluid and applied magnetic field in various regions around the piston and in multi-grooves are firstly investigated based on the model proposed by Case [46]. The dynamic viscosity of MR fluid is treated as constant when no magnetic fluid is applied and is described by continuous function when magnetic field is applied. Then the results are incorporated into COMSOL Multiphysics and double-sided magnetic fluid interaction simulations are performed. Finally, the simulation results are analyzed. The comparisons with experimental results are provided in section 4.
3.1.
Relationships between dynamic viscosity
and magnetic flux density
of MR fluid
3.1.1. The velocity relationships of various parts in the damper.
The components in the damper are ring column structures and can be divided as piston part and non-piston part. For the piston part, the radius of the piston rod is . For the non-piston part, the radii of both front and rear piston heads are
, and the radius of the middle coil is
. The inner radius of the damper housing is
. The values of the above-mentioned radii are listed in table 1. Different regions in the MR damper with multi-grooves are shown in figure 7. Region 1 refers to the region around piston rod, Region 2 is the new annular duct gap region, and Region 3 denotes the region around middle coil. Groove Region 1 and 2 are regions within the first- and second-layer multi-grooves, respectively.
Figure 7. Different regions in the MR damper with multi-grooves.
Download figure:
Standard image High-resolution imageWhen the piston moves, the piston velocity is . The velocities of MR fluid in Region 1, Region 2 and Region 3 are
,
and
, respectively. According to the volume flow balance, the relationships among these velocities are:

It is easy to know that according to the movement of the piston. Using the known values, equation (2) can be changed to:
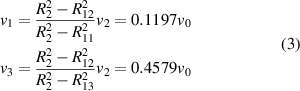
3.1.2. Relationships between shear rate.
and velocity
of MR fluid in various parts around piston To simplify expressions,
,
and
are now referred to as
. The radius variable is
. In a certain ring column segment of the damper, the initial pressure is
, the pressure drop is
, the length of the segment being analyzed is
, and the shear stress is
. The following equation holds:

Solving equation (4) based on the constant pressure gradient assumption, the following result is obtained:

Then, the shear rate of MR fluid is

Change the form of equation (6) for integration as

Combine equations (5) and (7) and integrate them on both sides:

The result of equation (8) is

Hence, the shear rate of MR fluid is

At different locations of , the shear rates
are different. To facilitate calculation, when
, the shear rate
at every
is substituted as the mean of the definite integral. Hence, average shear rate
is used to represent the shear rate at every
.
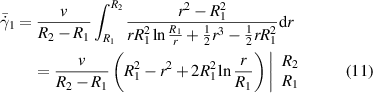
When , the value of this definite integral is divergent. Hence, the lower limit of the integral can be set as
.
is a small value that is used to prevent divergence. The value of
is dependent on the mesh size. According to the dimension of the mesh elements in our simulation, it is assumed that
is equal to the average length of the mesh elements in the radius direction, i.e.
.
When is restored to
,
,
and
is changed as
,
,
, respectively, the corresponding average shear rates are
,
and
, respectively. The numerical results of equation (11) at different locations are:
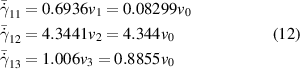
3.1.3. Relationships between shear rate.
,
and velocity
of MR fluid in multi-grooves In our design, there are two layers of circular shaped multi-grooves, whose inner and outer radii are
(
represents the number of layer,
means 'inner' and
means 'outer').
Take the first layer multi-groove (Groove Region 1) as an example. The radius variable is also , the length of the multi-groove is
, the pressure drop in the multi-groove is
, and the shear stress is
. Therefore, the driving thrust is
, and the flow resistance on the upper and lower walls is
. When the MR fluid flows in the multi-groove, the driving thrust and the flow resistance reach equilibrium.

By solving equation (13), one obtains

Similarly, at different locations of , the shear stresses
are different. To facilitate calculation, When
, the shear stress
at every
is substituted as the mean of the definite integral. Hence, average shear stress
is used to represent the shear stress at every
.

In equation (15), is the width of the first layer multi-groove. From the above analysis, the average shear stress in every layer of multi-groove is independent of the groove radius.
Similarly, in the second layer multi-groove (Groove Region 2), the average shear stress can be also expressed as:

where is the width of the second layer multi-groove.
Define the ratios of inner and outer radius as . The values of different
and
are listed in table 2.
Table 2. Values of different and
.
![]() |
![]() |
![]() |
---|---|---|
![]() |
![]() | |
![]() |
![]() |
![]() |
The outer radius of the multi-groove is represented as . Using the result of Bahrami et al [49], the average velocity
of MR fluid in the multi-groove is

Comparing equations (15)–(17), the average shear rate is
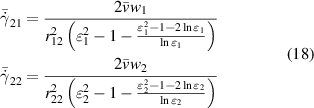
Substituting as
,
and substituting
as
,
respectively give the numerical results:

where is the average velocity of piston.
3.1.4. Relationships between dynamic viscosity.
and magnetic flux density
Numerical relationships between yield stress
and magnetic flux density
of MRF-132DG when external magnetic field is applied to MR fluid can be obtained from the work of Nguyen et al [50].

where the unit of is Pa and the unit of
is T.
Based on the results in Case et al [46], modified Bingham model is introduced.

In equation (21), is the dynamic viscosity of MRF-132DG when no magnetic field is applied. Parameters
and
are used to reflect the effect of magnetic field on dynamic viscosity. When
and
, modified Bingham model degenerates into classical Bingham model. In our simulation,
and
are selected, the same as the values used in [46].
When testing the MR damper, the excitation is sinusoidal whose displacement amplitude is and frequency
. Hence, the displacement function is

According to equation (22), the velocity function is

To simplify the model, the piston velocity and the average velocity of piston
are both unified as the average value of the velocity function in half a period, i.e.

Then the numerical expressions of dynamic viscosity at various parts are obtained by substituting equations (12), (19), (20) and (24) into equation (21):
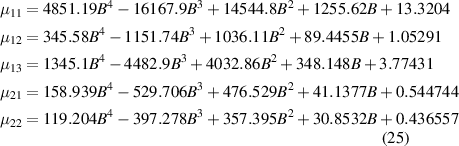
where ,
and
are dynamic viscosity of MR fluid in Region 1, 2, and 3, respectively;
and
are dynamic viscosity of MR fluid in Groove Region 1 and 2, respectively.
3.2. Multiphysics simulations using COMSOL Multiphysics
With good capability and adaptability in simulations of multi-fields, COMSOL Multiphysics was chosen as the simulation platform. Two dimensional CFD model was built in order to save calculation resource and time. As mentioned before, the motion of the piston was sinusoidal with amplitude of and frequency
. Transient analysis was performed with time step of 0.001 s and total time of 1 s. The applied currents were 0, 0.2 A, 0.4 A, 0.6 A, 0.8 A, 1.0 A, respectively. Equation (25) was input as the dynamic viscosity of MR fluid in different regions. The relative magnetic permeabilities of MR fluid, silicon steel and aluminum are 4, 1742 and 1, respectively [18]. Deformed mesh was used to simulate the sinusoidal motion of the piston. MR damper without and with multi-grooves were both simulated. The flow was regarded as laminar due to the low Reynold number. Parametric scanning was used to facilitate the simulations under various currents.
Fluid velocity and apparent viscosity of MR dampers without and with multi-grooves at different times when the current is 0.8 A are shown in figures 8 and 9, respectively. When the piston reciprocates in the cylinder, the MR fluid in the cylinder flows from one side of the piston to the other side through the gap and multi-grooves. When there are multi-grooves on the piston, less vortices are generated in the middle part of the piston, which results in more uniform velocity profiles. Although the volumetric displacement is similar in the two cases, much higher velocity around the piston with multi-grooves is observed in figure 8, which partly contributes to the higher yield stress and damping force. The higher velocity around the piston with multi-grooves is partly attributed to smaller apparent viscosity in figure 9, which expedites the MR fluid flow.
Figure 8. Fluid velocity of MR dampers without and with multi-grooves at different times when the current is 0.8 A. (A)–(C) MR damper without multi-grooves; (D)–(F) MR damper with multi-grooves; (A), (D) 0.07 s; (B), (E) 0.14 s; (C), (F) 0.21 s.
Download figure:
Standard image High-resolution imageFigure 9. Apparent viscosity of MR dampers without and with multi-grooves at different times when the current is 0.8 A. (A)–(C) MR damper without multi-grooves; (D)–(F) MR damper with multi-grooves; (A), (D) 0.07 s; (B), (E) 0.14 s; (C), (F) 0.21 s.
Download figure:
Standard image High-resolution imageFigure 10 depicts the magnetic flux density of MR dampers without and with multi-grooves at 0.21 s when the current is 0.8 A. In addition, the average magnetic flux densities in the gap and multi-grooves are calculated and listed in table 3. Although the magnetic flux densities in both cases are relatively uniform, the average magnetic flux density in gap with multi-grooves (Region 2) only decreases 4.18% compared with that in gap without multi-grooves, which can be negligible. More importantly, the average magnetic flux density in multi-grooves (Groove Region 1 and Groove Region 2) increases 15.6% compared with that in gap without multi-grooves. Hence, larger magnetic flux density is obtained in the active regions around the piston, which also partly contributes to the larger yield stress and damping force.
Figure 10. Magnetic flux density of MR dampers without and with multi-grooves at 0.21 s when the current is 0.8 A. (A) Without multi-grooves; (B) with multi-grooves.
Download figure:
Standard image High-resolution imageTable 3. Average magnetic flux density in the gap (without and with multi-grooves) and the multi-grooves at 0.21 s when the current is 0.8 A.
Gap (without multi-grooves) | Gap (with multi-grooves) (Region 2) | Multi-grooves (Groove Region 1 and Groove Region 2) | |
---|---|---|---|
Average magnetic flux density (T) | 0.263 | 0.252 | 0.304 |
3.3. Parametric analysis of multi-grooves
3.3.1. Revised simulation model for different configurations of multi-grooves.
Based on the multiphysics model and simulation methods mentioned above, parametric analysis of multi-grooves is now performed to further explore the influence of the multi-grooves. The parameters to be investigated are the number and width of the multi-grooves. According to the structure shown in figure 2, the following equation should be satisfied:

where is the number of multi-groove and the subscript
means the
th layer of multi-groove.
It is assumed that the circular wall should be as thin as possible to leave more space for the multi-grooves. Since the current circular wall is the thinnest wall that can be manufactured in the current stage, the thickness of the wall is treated as a constant in the following analysis.
Additionally, the width of the current design is assumed to be the upper boundary of
, i.e. the following constraint holds.

When the number and width of multi-groove are changed, the above-mentioned model for multiphysics simulation should be modified by treating the width of multi-grooves as variables. The numerical expressions of dynamic viscosity at Region 1, 2, and 3 remain the same as in equation (25).
The case is considered first as a general one. When the widths of multi-grooves are treated as variables, the ratios of inner and outer radius are
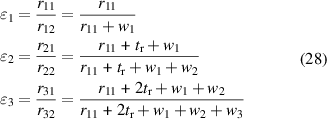
Then, based on equation (18), the average shear rates at Groove Region 1, 2, and 3 are obtained as
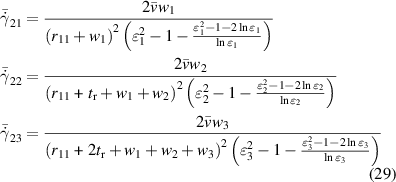
Finally, the numerical expressions of dynamic viscosity at Groove Region 1, 2, and 3 can be obtained by substituting equations (20), (24) and (29) into equation (21).
When , only
,
in equation (28) and
,
in equation (29) are used to derive the numerical expressions of dynamic viscosity at Groove Region 1 and 2. Similarly, when
, only
in equation (28) and
in equation (29) are used generate the numerical expressions of dynamic viscosity at Groove Region 1. It should be noted that the inner radius of the first-layer multi-groove
is different in the three cases in order to leave space for the circular ring(s), i.e.
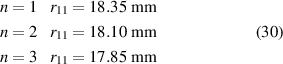
3.3.2. Influence of the number and width of multi-grooves.
According to the constraints in equations (26) and (27), different value combinations of ,
,
, and
were listed out at a step size of 0.05 mm for one-layer and two-layer cases and 0.1 mm for three-layer case. Then the revised simulation model was input into COMSOL Multiphysics. The applied current was 0.8 A and other configurations were the same as before. Parametric scan was used to investigate the influence of the number and width of multi-groove on the performance of the MR damper. The average magnetic flux density in gaps (Region 2) and multi-grooves (Groove Region 1, 2, and 3) were the evaluation indices.
3.3.2.1. One-layer multi-groove.
The average magnetic flux density at 0.21 s in gap (Region 2) and multi-grooves (Groove Region 1) under different multi-groove widths are plotted in figure 11. The average magnetic flux density in multi-grooves (Groove Region 1) increases maximally 10.4% (from 0.261 T to 0.289 T) compared with that in gap (Region 2) when , and the increment decreases to 6.47% (from 0.257 T to 0.273 T) when
. Meanwhile, the average magnetic flux density in multi-grooves (Groove Region 1) decreases when the multi-groove width increases.
Figure 11. Influence of multi-groove width on magnetic flux density in one-layer multi-groove case.
Download figure:
Standard image High-resolution image3.3.2.2. Two-layer multi-grooves.
The average magnetic flux density at 0.21 s in gap (Region 2) and multi-grooves (Groove Region 1 and 2) under different multi-groove widths are plotted in figure 12. When and
, the maximum average magnetic flux density in multi-grooves (Groove Region 1 and 2) is 0.326 T, which increases 25.6% compared with that in gap (Region 2) (red circle). When
and
, the minimum average magnetic flux density in multi-grooves (Groove Region 1 and 2) is 0.302 T, which increases 18.2% compared with that in gap (Region 2) (blue circle). Furthermore, with the increasing width of multi-grooves, the average magnetic flux density tends to decrease.
Figure 12. Influence of multi-groove width on magnetic flux density in two-layer multi-grooves case.
Download figure:
Standard image High-resolution image3.3.2.3. Three-layer multi-grooves.
The average magnetic flux density at 0.21 s in gap (Region 2) and multi-grooves (Groove Region 1, 2, and 3) under different multi-groove widths are plotted in figure 13, where the color bar represents the average magnetic flux density. The maximum average magnetic flux density in multi-grooves (Groove Region 1, 2, and 3) is 0.330 T when ,
, and
, which increases 29.9% compared with that in gap (Region 2) (red circle). The minimum average magnetic flux density in multi-grooves (Groove Region 1, 2, and 3) is 0.315 T when
,
, and
, which increases 21.9% compared with that in gap (Region 2) (blue circle). Additionally, the maximum average magnetic flux density in multi-grooves (Groove Region 1, 2, and 3) is getting larger when the width of multi-grooves decreases.
Figure 13. Influence of multi-groove width on magnetic flux density in three-layer multi-grooves case.
Download figure:
Standard image High-resolution imageIn summary, the average magnetic flux density in multi-grooves increases significantly when increasing the number and decreasing the width of multi-grooves, which further results in larger yield stress and damping force. This validates the idea to make small multiple annular flow gaps on piston. Although the multi-grooves with four layers or more layers are not considered, it can still be estimated that the average magnetic flux density in multi-grooves is larger than that of three-layer multi-grooves. Meanwhile, change of average magnetic flux density in gaps is relatively small when changing the number and width of multi-grooves.
4. Testing of MR dampers
The two MR damper prototypes without and with multi-grooves were fabricated and assembled. The testing platform was MTS 370 (Servo) Axial Torsional Material Testing System. The MR damper prototypes were installed using fixtures with special design. Since the MR damper will be used for prosthetic knee, sinusoidal excitations with amplitude of and frequency of
were applied so as to simulate human walking. A personal computer was used to control MTS 370 and record testing data. Different DCs were output to the MR damper by an electric power source in order to generate various magnetic fields. The output currents were 0, 0.2 A, 0.4 A, 0.6 A, 0.8 A, 1.0 A, respectively. Sensors built in MTS 370 were used to obtain force and displacement signals. The model of the load cell is 661.20F-01 with 25 kN force capability. The sampling frequency of the sensors is 200 Hz. Velocities of the MR damper were obtained through the first order finite difference of displacements. Figure 14 displays the experimental setup for testing MR damper.
Figure 14. Experimental setup of MR damper.
Download figure:
Standard image High-resolution imageFigures 15 and 16 give the force–displacement curves of MR dampers without and with multi-grooves. The continuous and smooth curves in the figures illustrate that there are no air bubbles in the MR damper. Maximum damping forces of MR damper under different currents are listed in table 4. When the current is equal to or larger than 0.4 A, the damping forces of the MR damper with multi-grooves are much larger than the ones without multi-grooves. This may as well be attributed to the higher velocity, magnetic flux density and smaller apparent viscosity as obtained by the simulations. Non-smooth transitions of force at high excitation currents (0.8 A and 1.0 A) are observed because the fixture becomes loose for a short period of time when damping forces are large.
Figure 15. Force–displacement curves of MR damper without multi-grooves.
Download figure:
Standard image High-resolution imageFigure 16. Force–displacement curves of MR damper with multi-grooves.
Download figure:
Standard image High-resolution imageTable 4. Maximum damping forces of MR damper under different currents.
![]() |
However, there is an exception case. When the current is 0.2 A, the damping force of the MR damper with multi-grooves is almost the same as the one when no current is applied. The damping force of the MR damper with multi-grooves is even less than the one without multi-grooves under the current of 0.2 A. Excluding operational and experimental errors, it is possible that the magnetic particle chains are not completely formed within small regions under low current. In other words, there might exist an 'activation current' for MR damper with multi-grooves. This is preliminary analysis, further investigations on this topic will be performed in the future.
In the simulation in section 3.2, the simulated stress in the axial direction was extracted and integrated over each moving surface of the piston to calculate the total damping force of the MR damper under each current. The simulated damping forces are plotted in the same figures and compared with the experimental data. Figure 15 shows the comparisons of MR damper without multi-grooves, while the MR damper with multi-grooves is compared in figure 16. From these figures, the simulation results agree well with the experimental ones though some deviations exist, which validates the effectiveness of the proposed model and the simulation methods. The absolute value of the relative error between simulation and experimental results at each point pair is calculated. These absolute values are then averaged under each current, i.e. average relative errors. The average relative errors between simulation and experimental results of MR damper without multi-grooves are 8.645%, 5.396%, 7.725%, 5.306%, 5.189%, 5.994% when currents are 0, 0.2 A, 0.4 A, 0.8 A, 1.0 A, respectively. The average relative errors between simulation and experimental results of MR damper with multi-grooves are 9.308%, 26.351%, 6.795%, 5.682%, 4.265%, 4.462% when currents are 0, 0.2 A, 0.4 A, 0.8 A, 1.0 A, respectively (As mentioned above, the experimental result of MR damper with multi-grooves under 0.2 A is exceptional). However, MR fluid flow in some small parts of regions around the piston may behave turbulent, while most of the MR fluid flow is laminar. The global laminar flow setting could not accurately characterize the behavior of MR fluid in these regions. Turbulence leads to fluctuations of different amplitudes, and fluctuations of large amplitudes make the curve discontinuous. Large fluctuations could be smoothed out by higher order numerical integration.
Using velocities obtained from the first order finite difference of the displacement data in figures 15 and 16 as the horizontal axis and the same experimental force data as vertical axis, the Force-Velocity curves of MR dampers without and with multi-grooves are plotted in figures 17 and 18, respectively. The damping force of MR damper is generally composed of three parts: field dependent force
, fluid viscous force
and mechanical friction force
, i.e.

Figure 17. Force–velocity curves of MR damper without multi-grooves.
Download figure:
Standard image High-resolution imageFigure 18. Force–velocity curves of MR damper with multi-grooves.
Download figure:
Standard image High-resolution imageFor a normal MR damper without multi-grooves, the expressions for the above-mentioned forces are


where is a coefficient depending on the MR fluid velocity;
and
are the piston and piston rod cross sectional areas, respectively;
is the dynamic viscosity of MR fluid.
In the force–velocity curve, when no current is applied and , the force is mechanical friction force
; when no current is applied, the maximum force is the sum of fluid viscous force and mechanical friction force
; when current is applied, the maximum damping force is the sum of fluid viscous force, mechanical friction force and field dependent force
. Different types of forces of MR damper without and with multi-grooves when current is 0 and 1.0 A are summarized in table 5. The ratio of the field dependent force with multi-grooves to the one without multi-grooves when current is 1.0 A is

Table 5. Types of forces of MR damper without and with multi-grooves when current is 0 and 1.0 A, respectively.
![]() |
If a normal MR damper without multi-grooves of similar configurations is built whose field dependent force is , the only way is to change the annular duct gap as
. At this time, the theoretical ratio of the fluid viscous force after change
to the one before change is (all the parameters are known)

However, according to the testing results, the experimental ratio of the fluid viscous force with multi-grooves to the one without multi-grooves is

It can be observed that , which provides a new idea to make MR damper. According to equations (32) and (33), the common method to increase the field dependent force is to decrease the annular duct gap
, but the fluid viscous force will also increase, which is unwanted. If some part of the annular duct gap
is fabricated as multi-grooves, the increment of fluid viscous force will be much less while keeping the same increase of field dependent force.
Moreover, mechanical friction force and fluid viscous force
are uncontrollable, while field dependent force
is controllable. Without multi-grooves, the damping force with no excitation current is
, the damping force under 1.0 A excitation current is
. Similarly, with multi-grooves, the damping force with no excitation current is
, the damping force under 1.0 A excitation current is
. The controllable force range of MR damper without multi-grooves is
and of MR damper with multi-grooves is
. From table 5, it is clear that MR damper with multi-grooves has much larger controllable force range (
). If the current continues to increase, the controllable force range will be larger. Because the damping force at 1.0 A is enough for prosthetic knee and larger current causes huge temperature rise, no larger currents were tested.
5. Discussions
- (a)Compared with the MR damper with inner bypass proposed by Bai et al [36], the benefit of this new MR damper with multi-grooves is that the structures can be compact. The damping force can be increased with the same energy consumption. Nevertheless, the main drawback of this design is the small increment of the viscous damping force.
- (b)Although the MR damper with multi-grooves performs better than the one without multi-grooves of similar configurations, the configurations and implementations of multi-grooves on MR damper are still preliminary. Although the two rings made of silicon steel are of good strength, it is still possible to break, which significantly compromises the service life of the MR damper. Our initial target is to fabricate grooves in micrometer scale on the piston. However, several concentric silicon steel slices were used to obtain multi-grooves (0.3 mm) in the current stage due to limitation of processing technology. The focus of our future work is to fabricate multi-grooves in micrometer scale on the piston, the so-called 'micro-grooves'. To realize this, advanced fabrication methods such as nano metal printing are to be used to fabricate multi-grooves with more layers with smaller width while having good strength and reliability. Multi-grooves would even be embedded into the piston without increasing parts. In addition, assembly methods with higher precision using some tools will also be utilized. Furthermore, the working mechanisms of MR fluid in micro-grooves also need to be studied. These mechanisms are not only limited in macroscopic mechanics, tribology and electromagnetics, but also are extended to microscopic behaviors of particles, which would be challenging. Other parameters that influence the performance of the MR damper could also be studied such as working frequencies and amplitudes.
- (c)In the proposed simulation model, several time and space average values are used to simplify calculations, which would cause errors. More precise model can be obtained by considering the time and space variables. In addition, the inner space of the MR damper is divided into separate regions, which might bring about discontinuity during calculation. Modeling of MR fluid as continuous medium would be another issue in future studies. Moreover, the proposed model is parametrically sensitive, which means that it is dependent on three parameters
,
and
. Parametric effect on the model accuracy could be further discussed.
- (d)Although special methods (PTFE + FKM) were used, the mechanical friction forces
in these two prototypes were still relatively large possibly due to manual assembling errors. Actually, the mechanical friction force
can be reduced to 38 N in another prototype of similar configurations and dimensions which is not shown here. Further investigations will be focused on ameliorating the assembly process and exploring better methods to decrease the mechanical friction force
so as to obtain larger controllable force range. Recently, some researchers investigated the durability and lubrication issues of MR damper [51–53]. Therefore, systematic studies on durability and lubrication of the proposed MR damper with multi-grooves will also be investigated by using more material combinations, establishing mathematical models, incorporating new structures, etc.
- (e)The MR damper developed in this work will be used as one of the driving unit for the smart prosthetic knee. The working principles of the smart prosthetic knee was proposed in [18], biomechanical and ergonomic design was then finished and prototype has been fabricated. In the next step, control algorithms for the MR damper and the smart prosthetic knee will be investigated, including the self-powered module. Clinical trials of the smart prosthetic knee on above-knee amputees will be conducted to evaluate its performances.
- (f)Although the current configuration in our design is not optimal according to the parametric analysis, it has already reached the size limit of normal machining and manual assembly. Additionally, further optimization can still be performed using PSO, neural network or genetic algorithm, etc. Then, some advanced methods for fabrication and assembly will be used to obtain precise and optimal structures in the future.
6. Conclusions
In this paper, a new MR damper with multi-grooves (small multiple annular flow gaps) on piston for performance enhancement was proposed. MR dampers without and with multi-grooves were designed, simulated, fabricated, and tested. Parametric analysis of the number and width of multi-grooves was performed. The advantages of MR damper with multi-grooves over the one without multi-grooves were validated by simulations and experiments. The main conclusions are as follows:
- (a)The damping force and controllable force range of MR damper with multi-grooves are larger than the one without multi-grooves possibly due to higher velocity, magnetic flux density and smaller apparent viscosity around the piston. When designing and fabricating MR damper, making multi-grooves can also decrease the increment of fluid viscous force while keeping the same increase of field dependent force.
- (b)The proposed coupled field model for multiphysics simulation accurately reflects the behaviors of MR fluid in different regions of MR damper. The simulation results are in good agreement with the experimental ones.
- (c)The parametric analysis reveals that larger average magnetic flux density in multi-grooves can be obtained by increasing the number and decreasing the width of multi-grooves.
Acknowledgments
This work is supported by the Innovation and Technology Commission (Project No. ITS/367/18) and Research Grants Council (Project No. CUHK 14210019) of Hong Kong Special Administrative Region, China and in part by Hong Kong Centre for Logistics Robotics of InnoHK. Experimental support from Department of Biomedical Engineering, City University of Hong Kong is gratefully acknowledged.