Abstract
Fire whirls can occur during urban fires, especially in intense fires in combustible building structures, and more often in forest or wildland fires. They are a special swirling diffusion flame characterized by significant enhancement in burning rates, flame heights and flame temperatures, along with a strong whirling motion of the flame. This whirling motion can pick up large firebrands and scatter them afar leading to spot fires. Many researchers have published experimental work on small- and medium-scale pool fire whirls and gaseous fuel fire whirls using split cylinders and various fixed-frame apparatus to investigate axial and tangential velocity profiles, axial and radial temperature distribution, burning rates, and flame heights. Likewise, several researchers have attempted to predict the experimental results of fire whirls using different modelling approaches and simulation software.
In this paper, experiments were undertaken to study the dynamics of propane gas fire whirls in a small-scale, square-based, fixed-frame apparatus. Measurements of flame height and temperature profiles (both axial centerline and radial) were made for a low initial momentum burner of 76.2 mm internal diameter. The burner was operated at a volumetric flow rate of 6 dm3/min, which gave a heat release rate of 9.12 kW. Simulations using Fire Dynamics Simulator (FDS 6.6.0) and ANSYS Fluent 17.1 were performed to compare with the experimental measurements. Four separate mesh refinements were employed and four different sub-grid-scale (SGS) turbulence models were tested with FDS. The Deardorff, Wall-Adapting Local Eddy-viscosity (WALE), and dynamic Smagorinsky models, formed stable fire whirls for the two largest mesh refinements.
The temperature profiles were overpredicted at the core of the flame with FDS and underpredicted with Fluent. The FDS simulation prematurely predicts the peak temperature for the axial centreline profile, whereas with Fluent the axial temperature profile matches the general trend of the experimental measurements.
The visible flame height, determined through image processing, was approximately 0.88 ± 0.06 m, which corresponds to a measured temperature of ∼500°C. The 500°C temperature contour was used as a rough approximation of the flame height in the numerical simulations. It was found that with Fluent the 500°C contour grew until the fire whirl stabilized and reached the top of the hood at 1.6 m, clearly overpredicting the flame height. The height estimates based on the predicted 500°C contours show a strong dependence on the mesh resolution. This is primarily due to increased instability resulting in more mixing and spreading of the temperature for the coarser mesh size. However, the simulated flame heights show less dependence on the SGS turbulence models.
Export citation and abstract BibTeX RIS
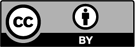
Content from this work may be used under the terms of the Creative Commons Attribution 3.0 licence. Any further distribution of this work must maintain attribution to the author(s) and the title of the work, journal citation and DOI.