Abstract
Sandwich composites with controllable cores have wide applications in aerospace structures. This paper presents a dynamic modeling and stability analysis of sandwich beams with a partially filled magneto-rheological (MR) fluid core covered by laminated composite face sheets in the supersonic flow regime. The equations of motion of the resulting system are formulated using energy expressions and the Hamilton principle. Finite element modeling is employed to solve the equations with different boundary conditions. Initially, free vibration analysis is performed and the effect of the magnetic field on the natural frequencies of the beam is reported. In order to minimize the weight, the magnetorheological fluid is filled at selected cells in the core layer. The locations and sizes of these cells affect the modal characteristics and flutter stability of the beam. Also, the impact of core layer thickness under different boundary conditions is studied. Furthermore, the influence of magnetic field on the critical pressure in supersonic flow regime is investigated using first-order piston theory to identify the unstable regions. The results revealed that the size and position of the MR section in the beam and the applied magnetic field strength drastically influence the natural frequencies of partially treated magnetorheological laminated sandwich beams. The influencing variables are identified from main-effect plots using analysis of variance study.
Export citation and abstract BibTeX RIS
1. Introduction
The sandwich structures made of composite materials are widely employed in automotive and aerospace applications, due to their high stiffness, strength-to-weight ratio, durability, and low maintenance cost. Such exposed skin of aerospace vehicles, vehicle body parts structures are often subjected to various types of loads and undergo resonances and flutter failures. Dynamic analysis of such structures is therefore of paramount importance before commissioning them. In practice, the core region is made-up of soft material where the shear effect dominates. Stiffness properties can be altered in the face layers similar to the damping characteristics in the core layer. The homogeneous face sheet sandwich structures with viscoelastic core were studied widely over the past two decades (Hu et al 2008, Araújo et al 2010, Arikoglu and Ozkol 2010, Bilasse et al 2010, Moita et al 2011). With the advent of smart structure technology and the development of a wide range of integrated multifunctional materials, the dynamic performance of the sandwich structures has improved tremendously. The semi-active vibration suppression technology with the use of rheological fluids and shape memory alloys in recent times drastically enhanced the damping behavior of integrated structures in comparison with viscoelastic materials. The characteristics of smart structures like damping and stiffness can expeditiously change by applying external magnetic or electric fields. Magneto-rheological (MR) fluids in comparison with electro-rheological (ER) fluids produce higher yield strength and are less sensitive to temperature fluctuations and impurities (Weiss et al 1994). Sandwich beams with MR fluid or elastomeric cores became very popular in recent times for vibration control applications over a frequency range.
Yalcintas and Dai (1999, 2003) studied the MR fluid embedded sandwich structures analytically and experimentally and, compared them with ER fluid embedded sandwich structures. The results show MR fluid structures performed twice as good as those with ER fluid core. For MR fluid sandwich beam, Sun et al (2003) established a relation between the complex shear modulus and magnetic field intensity and correlated experimental data with analytical results. Yeh and Shih (2006) studied the dynamic characteristics of a magnetorheological sandwich beam when subjected to harmonic load. Lara-Prieto et al (2009) carried out experiments to explore the vibration behaviour on cantilevered sandwich beam with core as magnetorheological fluid and demonstrated vibration control using magnetic field strengths. Rajamohan et al (2009, 2010a, 2010b) computed the governing equations for magnetorheological sandwich beam and obtained an approximate solution using the Ritz method. They introduced the concept of partially treated MR core layer to reduce structural weight and further studied the optimal positioning of these MR segments for vibration suppression of clamped-free beam via linear quadratic regulator control. Under periodic axial load, Nayak et al (2011, 2013) derived the equations of motion of a sandwich beam using Hamilton's principle and obtained solutions using Galerkin's technique. The beam has of MR elastomer (MRE) viscoelastic core and a conductive skin and their findings showed that with viscoelastic MR elastomer materials, the vibration levels were reduced by 30% in comparison with not using them. Dyniewicz et al (2015) analysed the partially treated MR elastomer sandwich beam with elastic face sheets and developed semi-active control strategy. They demonstrated that, by implementation of control technique, the stiffness and damping of a magnetorheological elastomer sandwich beam can be increased. In addition, (Nayak et al 2014, Navazi et al 2017, Arumugam et al 2019) looked at the vibration analysis of rotating magnetorheological sandwich beams. Aguib et al (2014) analysed the dynamic behaviour of sandwich plates with an MRE core and varied ferromagnetic micrometric particle loads under the influence of varying magnetic field intensities using computational and experimental methods. Yeh (2013) considered a magnetorheological elastomer sandwich plate to understand its vibrational behaviour. Different magnetic field strengths were considered to understand their influence on fundamental frequencies and loss factors of the sandwich plate. The dynamic behaviour of magnetorheological fluid laminated composite sandwich plates that had been partially and fully treated was studied by Manoharan et al (2014) and Ramamoorthy et al (2016). Under varied magnetic field intensities, the loss factor and natural frequency of laminated composite plates were investigated. Further, the effect of magnetorheological fluid layer thickness and orientations of the ply has also been studied. Eshaghi et al (2015, 2017) measured the dynamic behaviour of MR fluid as the core layer sandwich plates. In another work, the optimal locations of MR fluid pockets in a plate were determined by taking into account the influence of slippage between the layers of the structure and in reaction to a magnetic field, optimized the damping ratios and natural frequencies. Babu and Vasudevan (2016) and Vemuluri et al (2018) obtained the vibration characteristics for a partly and fully treated tapered laminated composite MR elastomer sandwich plate by analytical and experimental methods and the effects of ply orientation, taper angle, resin placement, and MR elastomer segment's location on natural frequencies were reported. Recently, Rokn-Abadi et al (2020) analyzed the influence of magnetic fields for different magnetorheological elastomer materials on the dynamic stability of a sandwich beam when subjected to a follower force under various boundary conditions. Most of the researchers considered MR fluids rather than MRE, the effect of magnetic field intensity will be instantaneous on MR fluids when compared to MR elastomer in the practical scenario. So, in this article MR fluid is considered.
Flutter is aeroelastic instability in structures occurring at certain flow velocities due to the interaction of an aerodynamic flow with the elastic modes of a mechanical structure. For the last few decades, flutter stability studies of composite structures have become an active area of research to avoid catastrophic failures. Asgari et al (2016, 2019) investigated the flutter instabilities of partially and fully treated magnetorheological fluid sandwich beams in supersonic flow conditions. The influence of magnetic field strength, constraining layer, and core layer thicknesses on the critical aerodynamic pressure were investigated for various boundary conditions of the beam. Bornassi et al (2018) investigated the effect of MR fluid on the aeroelastic stability of turbomachinery blades. It was concluded that the flutter velocity of turbomachine improves with consideration of MR fluid core materials. The flutter analysis of magnetorheological sandwich plates treated fully and partially was investigated by Eshaghi (2020a, 2020b). The optimal positioning of MR pockets in sandwich plates was obtained in order to maximize the boundary region of the flutter for the magnetorheological sandwich plate. In spite of above works dealing with the aeroelastic properties of magnetorheological sandwich structures, the studies on MR core laminated composite structures need thorough investigations. The flutter analysis of composite sandwich structures in different flow regimes is also an important objective. The current research looks into the vibrational and flutter analysis of a composite MR sandwich beam operating in supersonic flow conditions. By considering the partially treated MRF pockets in the core region of sandwich beam, the natural frequencies and free vibration response is obtained for different boundary conditions. Further, the impact of applied magnetic field on the aerodynamic pressure intensities is also studied. All the effective input variables are identified and ANOVA studies are conducted to predict the most influencing variables on fundamental frequency and critical aerodynamic pressure. The remaining part of the paper is organized as follows: The energy expressions used to derive the equations of motion are briefly presented in the mathematical modelling section. Numerical results of different configurations of composite face layer along with parametric studies are presented in the results and discussion section. In addition, analysis of variance studies on the two output quantities are presented with detailed full factorial experiments. Brief conclusions of the work are highlighted in the conclusions part.
2. Mathematical modelling
The Finite Element Formulation For A laminated sandwich beam with partially treated core configuration can be represented based on a fully treated laminated sandwich beam(Rajamohan et al 2010a). Consider multiple MR fluid segments embedded in the laminated sandwich beam's middle or core layer. To achieve compliant deformation and the continual responsiveness of the composite structure, the MR-fluid segments can be modelled separately and then combined with the adjacent segments. As illustrated in figure 1, the core layer of the sandwich beam treated partially has three sections. The composite layer is present in the first and last segments of lengths L1 and L3, respectively, and the MR fluid layer is present in the middle segment of length L2.
Figure 1. MR fluid segment of laminated sandwich beam.
Download figure:
Standard image High-resolution imageFor mathematical modelling purposes, following assumptions are made: (i) no slip between the top, bottom and core layers (ii) the MR layer has negligible normal stresses due to its low elastic modulus and (iii) in all the layers, the transverse displacement is same.
The transverse and longitudinal displacements of composite layers at any point (x, z) on beam can be described using the assumptions stated above as (Reddy 2003).


where ut,b and w are respectively the displacement components along the x and z directions and the relation between top and bottom layers (Rajamohan et al
2010a) is such that where
The shear strain γ in the MR layer can be derived as.

Where d = ½ (2hc+ht+hb), here h indicates the thickness of the layer and suffixes t, c, b, are top, core and bottom respectively.
MR fluid behaves as viscoelastic material in the pre-yield region, which is expressed as the magnetic field(B) dependent complex shear modulus (Asgari and Kouchakzadeh 2016) as.

Where G1 and G2 are the shear storage modulus and loss modulus, respectively given as: G1 = 3.3691B2 + 4.9975B × 103 + 0.873 × 106 and G2 = 0.9B2 + 0.8124 B × 103 + 0.1855 × 106.
The corresponding in-plane force and bending moment in the face layers are given by:

where, A11, B11, and D11 are the extension, coupling and bending stiffness parameters given as:

Here n is the number of plies of each face layer and is the transformed stiffness matrix.
Hamilton's equation is employed to derive the equations of motion for the laminated sandwich beam. The laminated MR sandwich beam's overall strain energy (U) can be written as the summation of the strain energies related to the top (Ut), core (Uc), and bottom (Ub), layers as.

The strain energy due to the laminated sandwich beam's top and bottom layers, can be represented as follows:

where is extensional stiffness coefficients of top layer,
is extensional stiffness coefficients of bottom layer,
are bending stiffness coefficients of top layer,
bending stiffness coefficients of bottom layer, L is the length of the beam and b is the width of the beam. The strain energy of the core layer UC is the combination of composite layer of length L1, MR fluid layer of length L2 and composite layer of length L3 can be expressed as
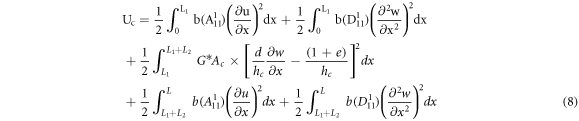
The kinetic energy of the laminated MR sandwich beam is estimated by accounting for the lateral deformation, longitudinal deformations and rotational deformation. As a result, the laminated sandwich beam's total kinetic energy T is given as

The kinetic energy generated by the top, bottom, and core layers lateral deformation can be represented as

where ρ is density of composite material, A is the area of the cross-sections and the suffixes t, b and c indicate respectively top, bottom and core layers. The kinetic energy obtained with the top and bottom composite layer's longitudinal deformation (T2) and the magnetorheological core layer rotational deformation (T3) can be written as


On the top surface of the beam, aerodynamic pressure is applied by air flowing in the x-direction. The work done by the aerodynamic pressure is given as

is the aerodynamic pressure, it is described based on the piston theory as

where M∞
is Mach number, V∞
is free stream velocity, ρ∞
Air density, is a constant value indicates non-dimensional aerodynamic pressure. The non-dimensional aerodynamic pressure (λ) parameter is used to determine the flutter border.
A typical 2-node beam element with three degrees of freedom per node, namely transverse displacement (w), angular displacements (θ) and axial displacement (u) is employed to discretize the beam. The axial and transverse displacement functions are written in terms of shape functions and displacement vectors as


where Nu(x) and Nw(x) are shape functions and d(t) = [ui, wi, θi, ui+1, w i+1, θi+1] T is displacement vector. By inserting equations (15) and (16) into equations (6) and (9), and then into the Hamilton's equations.

The formulated governing equations of motion for an elemental undamped laminated sandwich beam treated partially with magnetorheological fluid is

where [m] is the elemental mass matrix and [k] is the elemental stiffness matrix and f is the element nodal force vector. The global equation of magnetorheological laminated composite sandwich beam is given as

The assembled matrices [M] and [K] for a partially treated laminated sandwich beam are formulated by enforcing compatibility constraints in the intermediate layer of the beam that imposes on the composite material and MR fluid section interfaces. The [C] = α[M]+β[K] represents the material damping matrix. Where α and β are the material constants obtained from natural frequency and damping ratio values (Song and Su (2017)). Due to complex shear modulus considerations for the MR fluid core material, the assembled mass matrix is complex resulting in the complex conjugate eigenvalues.
3. Computational results and discussion
The free vibration and flutter study analysis are studied using a computer code written in Matlab and initially the results are validated with the homogeneous sandwich beam by considering material and geometrical properties from literature (Nayak et al 2011, Navazi et al 2017). The convergence study is performed to identify optimum number of elements. Figure 2 shows that the 24-element configuration is ideal and employed through-out the analysis.
Figure 2. Convergence curve of composite MR fluid sandwich panel.
Download figure:
Standard image High-resolution imageThe first three natural frequencies are obtained for different magnetic field intensities as depicted in table 1 and are found in good agreement with published results. The deviation of natural frequencies at higher modes may be with the present classical theory.
Table 1. First three modes of magnetorheological sandwich beam.
Magnetic field | Mode | Ritz method (Navazi et al 2017) | Analytical method (Nayak et al 2011) | Present |
---|---|---|---|---|
0 | 1 | 14.19 | 14.43 | 14.24 |
2 | 51.13 | 51.84 | 51.39 | |
3 | 104.28 | 105.05 | 104.36 | |
0.2 | 1 | 15.52 | 15.77 | 15.59 |
2 | 58.4 | 59.15 | 58.9 | |
3 | 120.59 | 121.12 | 120.92 | |
0.4 | 1 | 16.36 | 16.64 | 16.45 |
2 | 64.32 | 65.15 | 65.09 | |
3 | 134.58 | 135.02 | 135.29 | |
0.6 | 1 | 16.59 | 16.87 | 16.67 |
2 | 66.23 | 67.11 | 67.1 | |
3 | 139.23 | 139.73 | 140.12 |
For validation of flutter analysis, the material and geometry considered are from reference(Asgari and Kouchakzadeh 2016). The variation of critical aerodynamic pressure with present method and those reported by Asgari et al (2019) for MR sandwich beam under different magnetic fields are listed in table 2 and there is good agreement amongst the results.
Table 2. Comparison of flutter frequencies with magnetic field intensities.
Magnetic field intensity (Gauss) | Critical aerodynamic pressure | ||||
---|---|---|---|---|---|
0 | 100 | 200 | 300 | 400 | |
Present | 350 | 371 | 396 | 412 | 429 |
Asgari et al (2016) | 344 | 380 | 400 | 420 | 430 |
Error %age | −1.7 | 2.3 | 1 | 1.9 | 0.23 |
Many factors influence the aeroelastic characteristics of laminated sandwich beam with magnetorheological fluid as core, including magnetic field intensity, core layer thickness, beam size, and boundary conditions. The finite element approach is employed in this study to examine the influence of MR fluid layer thickness on aerodynamic pressure under varied magnetic field strengths, as well as the position and size of MR fluid sections. In this article, four combinations of MR damping treatments of laminated sandwich beams were considered, labelled 'A' to 'D' as illustrated in figure 3. Asgari et al (2019) said in their conclusion that MR segments should not be placed in the center of the panel to boost critical aerodynamic pressure. So, in this paper four configurations are considered which are concentrated at the end conditions. The laminated sandwich beam's overall length is divided into 24 segments of the same length, 6 segments of which are treated with MR fluid at selected parts of the structure and the rest segments are of composite material.
Figure 3. Four configurations of MR fluid sandwich panel.
Download figure:
Standard image High-resolution imageThe material properties of the partially treated MR fluid core with laminated face layer sandwich beam are considered from Manoharan et al (2014). The MR fluid with density ρc = 3500 kg m−3 is considered and it constitutes silicone oil and micro-sized iron particles. Its properties will vary based on the concentration of iron particles. In the present work, MR fluid properties are considered from Asgari et al (2019). The composite laminated face sheets are considered with layup configuration [0/90/90/0]. Each face sheet and core have a geometric dimension of 300 mm × 30 mm × 1mm each.
For clamped-clamped and simply supported conditions, the first five modes of four configurations A, B, C, D are compared with laminated sandwich beam which is fully treated with MR fluid core are shown in table 3.
Table 3. First four natural frequencies of clamped-clamped and simply supported boundary condition.
Boundary conditions | Mode | Fully treated (Hz) | Configuration 'A' (Hz) | Configuration 'B' (Hz) | Configuration 'C' (Hz) | Configuration 'D' (Hz) |
---|---|---|---|---|---|---|
C-C | 1 | 79.96 | 99.17 | 98.79 | 100.65 | 99.93 |
2 | 211.66 | 267.14 | 278.40 | 267.33 | 261.07 | |
3 | 407.11 | 516.78 | 534.91 | 507.37 | 528.95 | |
4 | 666.42 | 875.93 | 856.33 | 851.43 | 848.80 | |
S-S | 1 | 40.15 | 45.73 | 46.85 | 45.28 | 42.205 |
2 | 130.88 | 157.56 | 161.51 | 154.44 | 152.07 | |
3 | 280.38 | 347.35 | 338.36 | 342.02 | 353.43 | |
4 | 489.40 | 621.82 | 592.16 | 626.72 | 603.78 |
All configuration's natural frequencies are greater than the fully treated beam for clamped-clamped condition in which configuration 'C' has the highest value, similarly for simply supported condition the frequencies in all configurations are greater than those in fully treated core beam in which configuration 'B' has the highest value. Based upon the application, we can select a right configuration.
The influence in variation of magnetic field for fully and partially treated MR embedded composite sandwich beam with respect to natural frequency is listed in table 4. It is observed from the results that natural frequency of first mode is increasing while the magnetic field intensity increases. In fully treated beam, percentage of increment in natural frequency by applying magnetic field is high when compare to partially treated configurations. This is because we considered only one-fourth length of the beam is treated with MR Fluid.
The natural frequencies and loss factor of fully treated MR layer beam with respect to non-dimensional aerodynamic pressure (λ) under 200 G magnetic field intensity are shown in figures 4(a) and (b) for clamped-clamped condition.
Figure 4. (a) Non-dimensional aerodynamic pressure varying with natural frequencies and (b) Non-dimensional aerodynamic pressure varying with loss factors at 200 Gauss for clamped-clamped condition fully treated.
Download figure:
Standard image High-resolution imageSimilarly, natural frequencies and loss factor for configuration 'B' with clamped-clamped boundary condition and simply supported under 200 G magnetic field intensity are shown in Figures 5(a) and (b) and 6(a) and (b) respectively. It has been noticed that first two modes of the sandwich beam are closely spaced but do not coalesce due to damping of the MR fluid layer and also it is observed that flutter instability occurs between the first two modes of the system irrespective of the boundary condition.
Figure 5. (a) For configuration-C, Non-dimensional aerodynamic pressure varying with natural frequencies and. (b) Non-dimensional aerodynamic pressure varying with loss factors pressure at 200 Gauss for clamped-clamped beam.
Download figure:
Standard image High-resolution imageFigure 6. (a) For configuration-B, Non-dimensional aerodynamic pressure varying with natural frequencies and. (b) Non-dimensional aerodynamic pressure varying with loss factors at 200 Gauss for simply supported condition.
Download figure:
Standard image High-resolution imageFor different configurations of the simply supported laminated magnetorheological sandwich beam, figure 7(a) displays the impact of magnetic field intensity on non-dimensional aerodynamic pressure(λ). Similarly figure 7(b) shows for clamped-clamped condition. In all configurations, as the magnetic field intensity increases, so does the non-dimensional aerodynamic pressure. Configuration's 'B' and 'C' have the lowest and highest critical aerodynamic pressures, respectively. The difference between the first two natural frequency may be seen to be precisely proportional to critical aerodynamic pressure. Figure 8 shows the critical aerodynamic pressure as a function of magnetic field intensity for different values of the core layer thicknesses (h.c.). Here, the simply supported boundary conditions for the configuration-C are considered. It is observed that the non-dimensional aerodynamic pressure (λ) increases with increase of the core layer thickness (h.c).
Figure 7. Variation of Magnetic field intensity versus non-dimensional aerodynamic for various configuration under (a) S-S condition (b) C-C condition.
Download figure:
Standard image High-resolution imageFigure 8. Variation of non-dimensional aerodynamic pressure with magnetic field intensity.
Download figure:
Standard image High-resolution imageTable 4. Variation of Magnetic field intensity with respect to natural frequency for different configurations and boundary conditions.
Boundary condition | Magnetic field Intensity (Gauss) | 0 | 250 | 500 |
---|---|---|---|---|
Clamped-Clamped | Fully | 79.96 | 86.83 | 90.64 |
Config 'A' | 99.17 | 101.25 | 102.46 | |
Config 'B' | 98.79 | 100.55 | 101.56 | |
Config 'C' | 100.65 | 103.04 | 104.43 | |
Config 'D' | 99.93 | 102.35 | 103.75 | |
Simply Supported | Fully | 40.15 | 49.70 | 54.58 |
Config 'A' | 45.73 | 50.52 | 53.14 | |
Config 'B' | 46.85 | 51.99 | 54.75 | |
Config 'C' | 45.28 | 49.94 | 52.49 | |
Config 'D' | 42.20 | 45.59 | 47.48 |
The ply orientation may also affect the critical aerodynamic pressure. Under a constant magnetic field strength of 400G, the two-ply orientations (0/90/90/0/MR/0/90/90/0) and (45/-45/-45/45/MR/45/-45/-45/45) are considered for both simply supported and clamped-clamped boundary conditions, the natural frequencies of all the configurations are obtained. Table 5 depicts these results.
Table 5. Effect of ply orientation on the natural frequencies (Hz).
Ply orientation | Mode | B.C | Fully treated | Config 'A' | Config 'B' | Config 'C' | Config 'D' |
---|---|---|---|---|---|---|---|
0/90/90/0/MR/0/90/90/0 | 1 | SS | 53.08 | 52.33 | 53.89 | 51.69 | 46.89 |
2 | 148.13 | 162.42 | 167.51 | 158.52 | 155.29 | ||
3 | 299.06 | 351.63 | 341.94 | 345.55 | 358.41 | ||
1 | CC | 89.45 | 102.08 | 101.24 | 103.99 | 103.31 | |
2 | 225.51 | 269.95 | 282.26 | 270.41 | 263.74 | ||
3 | 422.80 | 519.51 | 538.95 | 509.83 | 533.82 | ||
45/-45/-45/45/MR/45/-45/-45/45 | 1 | SS | 46.73 | 38.63 | 39.57 | 38.17 | 33.09 |
2 | 108.52 | 96.17 | 100.98 | 92.82 | 89.34 | ||
3 | 194.73 | 196.48 | 190.16 | 191.78 | 201.66 | ||
1 | CC | 63.85 | 60.23 | 58.66 | 62.04 | 61.80 | |
2 | 146.19 | 150.00 | 158.51 | 150.84 | 146.37 | ||
3 | 256.67 | 283.19 | 296.36 | 277.55 | 295.30 |
Here, we can observe that ply orientation [45/-45]2 has relatively smaller natural frequencies compared to cross ply orientation irrespective of boundary conditions. For [45/-45]2 ply orientation, all configurations natural frequencies are less compared to fully treated MR composite sandwich beam irrespective of boundary conditions. But for [0/90]2 ply orientation, configuration-C produces high natural frequency than the fully treated MR core sandwich beam for clamped-clamped condition, whereas for simply supported Configuration-B has higher natural frequency.
Further critical aerodynamic pressure is calculated for clamped-clamped condition by considering the ply orientations and magnetic field intensity 400G which is listed in table 8.
From results, it is observed that config C has higher flutter instability boundary point compared to other configurations irrespective of ply orientation. For [45/-45]2 ply orientation, fully treated MR composite sandwich beam gives the higher flutter boundary point when compare to its all configurations but, which is not in the case of [0/90]2 ply orientation where fully treated is less than all other configurations. Table 6 also shows the critical natural frequencies, at which loss factor changes from positive to negative then flutter region starts.
Table 6. Effect of ply orientation on the non-dimensional aerodynamic pressure.
0/90/90/0/MR/0/90/90/0 | 45/-45/-45/45/MR/45/-45/-45/45 | |||||
---|---|---|---|---|---|---|
Natural Frequency (Hz) | Critical Aerodynamic pressure | Natural Frequency (Hz) | Critical Aerodynamic pressure | |||
f1 | f2 | λ | f1 | f2 | λ | |
Fully | 134.16 | 222.84 | 1140 | 91.184 | 147.72 | 494 |
Config 'A' | 194.2 | 252.59 | 1585 | 108.97 | 140.76 | 474 |
Config 'B' | 184.06 | 270.93 | 1548 | 102.52 | 152.9 | 464 |
Config 'C' | 197.55 | 252.48 | 1602 | 111.18 | 141.45 | 480 |
Config 'D' | 181.09 | 250.15 | 1488 | 102.97 | 139.2 | 456 |
Number of laminates in the face layers of the composite sandwich beam also influences the flutter instability region. So, we have simulated with two to five layers with cross ply orientation and symmetric. Results are listed in table 7 for various configurations under 400 G magnetic field intensity in clamped-clamped conditions. From results, it is observed that three-layer laminate sequence (0/90/0) has obtained higher flutter stability irrespective of various configurations and the configuration-C has higher flutter stability region compared to all configurations by varying the number of layers.
Table 7. Effect of number of laminates on the non-dimensional aerodynamic pressure.
Ply orientation | Fully treated | Config 'A' | Config 'B' | Config 'C' | Config 'D' |
---|---|---|---|---|---|
0/90 | 785 | 979 | 956 | 989 | 924 |
0/90/0 | 1224 | 1728 | 1686 | 1746 | 1620 |
0/90/90/0 | 1140 | 1585 | 1548 | 1602 | 1488 |
0/90/0/90/0 | 1061 | 1451 | 1417 | 1466 | 1363 |
4. Analysis of variance (ANOVA)
The method of Taguchi design of experiments facilitates in studying finally the impact of each individual parameter on the outputs under consideration. Various analytical techniques are used to make decisions about which parameters affect the response of the research process. The most common statistical approach for interpreting experimental data will be analysis of variance due to its accuracy (Pulido-Gonzalez et al 2020). The primary purpose of analysis of variance (ANOVA) is to indicate the significance order of the contributing factors to the response. This statistical approach allows us to determine how parameters interact with one another and to assess their relevance. In order to observe the overall effects of each parameter on first mode and critical pressure, 3 parameter-3 level design of experiments are considered for configuration 'C'. The three parameters considered are (i) ply orientation, (ii) magnetic field intensity, (iii) core layer thickness which are listed in table 8. The face layer thickness in all cases is kept as 1 mm. The full factorial experiments (i.e., 27 experiments) are conducted and the results were obtained, which are used for the ANOVA.
Table 8. Three levels of design parameters.
Notation | Design parameter | Level 1 | Level 2 | Level 3 |
---|---|---|---|---|
P | Ply orientation | 0/90/90/0 | 0/90/0/90 | 45/-45/-45/45 |
B | Magnetic field intensity (Gauss) | 0 | 250 | 500 |
T | Core thickness | 0.5 | 1 | 2 |
The main effect plots for fundamental natural frequency and critical aerodynamic pressure are shown in figures 9(a) and (b). The average value is indicated by the dotted horizontal line. The findings of the analysis permitted the following conclusions to be drawn with respect to natural frequency and critical aerodynamic pressure: With higher the best criteria, the parametric levels 1, 3, 1 respectively for ply orientation, magnetic field intensity and the core layer thickness give the maximum natural frequency and critical aerodynamic pressure.
Figure 9. (a) Main effects plot for natural frequency. (b) Main effects plot for critical aerodynamic pressure.
Download figure:
Standard image High-resolution imageIn the analysis of variance, the summary table consisting of degree of freedom (DF), sum of squares (SS), Mean of squares (MS), F-ratio (F), probability of the null hypotheses (p) is employed. If the probability of the null hypotheses (p) value is greater than 0.05, then there will be no significance of design variables to the output results (Pulido-Gonzalez et al 2020) and higher the 'F' value indicates that design parameter has most significant effect on the outcomes. Table 9 shows the effect of parameters on the fundamental frequency and critical aerodynamic pressure.
Table 9. Analysis of Variance for fundamental frequency and critical aerodynamic pressure.
Source | DF | Adj. SS | F-value | p-value | Contribution percentage | |
---|---|---|---|---|---|---|
Natural frequency | Ply-orientation | 2 | 33661.3 | 6973.42 | 0.00 | 99.15 |
Magnetic field intensity | 2 | 88.7 | 18.38 | 0.00 | 0.26 | |
Core thickness | 2 | 150.7 | 31.22 | 0.00 | 0.44 | |
Error | 20 | 48.3 | 0.14 | |||
Total | 26 | 33949 | ||||
Critical aerodynamic pressure | Ply-orientation | 2 | 5614956 | 15186.20 | 0.000 | 99.72 |
Magnetic field intensity | 2 | 2500 | 6.76 | 0.006 | 0.04 | |
Core thickness | 2 | 9780 | 26.45 | 0.000 | 0.17 | |
Error | 20 | 3697 | 0.06 | |||
Total | 26 | 5630933 |
The contribution percentage of parameters to the fundamental frequency is ply orientation (99.15%), core layer thickness (0.44%) and magnetic field intensity (0.44%). Similarly, the contribution percentage of design variables to the critical aerodynamic pressure is ply orientation (99.72%), core layer thickness (0.04%) and magnetic field intensity (0.17%). It is observed that the ply orientation factor contributed has a vital effect on outputs, followed by core layer thickness and magnetic field intensities.
5. Conclusions
In the present work, the damping performance of fully and partially filled MR fluid core-laminated composite sandwich beams was investigated in supersonic flow conditions. The influence of position of the MR fluid segments on dynamic characteristics and stability of laminated composite sandwich beam has been studied. The locations were considered arbitrarily in the work; however, their selection may be based on different criteria such as parametric optimization, antinodes in the mode shapes, etc. Apart from location of MR segments, other parameters like thickness of the core layer, the magnetic field intensity and face layer ply orientation have vital effect on flutter boundaries. Following are some conclusions drawn from the work:
- 1.Regarding the locations of MR fluid segments considered, the C-configuration gives a better result than other configurations in a clamped-clamped condition whereas it is B-configuration for simply-supported condition.
- 2.The variation in the thicknesses of the core layer was also slightly influencing the non-dimensional aerodynamic pressure for all four configurations for both clamped- clamped and simply supported boundary conditions.
- 3.The magnetic field intensity is proportional to critical aerodynamic pressure for all configurations, regardless of core layer thickness and ply orientation for various boundary conditions.
- 4.At the laminated composite face layer, the cross ply configuration leads to more flutter stability than the angle ply orientations. Further, number of plies of composite laminate also significantly influences the flutter stability. Of all the configurations, three layered composite laminate gives a better result.
- 5.From the ANOVA study with considered levels of variables, the ply orientation has relatively higher influence on both natural frequency and critical aerodynamic pressure, its contribution percentage is more than 99%. Next to that core layer thickness has considerable influence on stability and it contributes to 0.5%.
Data availability
All data that support the findings of this study are included within the article (and any supplementary files).
Funding
This research received no specific grant from any funding agency in the public, commercial, or not-for-profit sectors.
Conflict of interest
The authors declare no conflict of interest in preparing this article.